Scalable Business for Startups
Get the oars in the water and start rowing. Execution is the single biggest factor in achievement so the faster and better your execution.
QMS
Quality Management System (QMS)

Overview
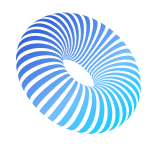
"Quality Management System "
In the pharmaceutical manufacturing industry, managing instrument and column usage logs is crucial for ensuring compliance, data integrity, and efficient operations. Such software typically includes features for

Incident Management
This module allows the documentation and tracking of incidents that occur during the manufacturing process. It includes features for:
- Recording incident details
- Classifying and prioritizing incidents
- Investigating root causes
- Implementing corrective actions
- Monitoring and closing incidents
Deviation Management
This module manages deviations from standard operating procedures (SOPs) and other predefined processes. It helps in:
- Logging deviations
- Assessing the impact of deviations
- Investigating causes
- Approving deviation reports
- Implementing corrective actions
Corrective and Preventive Actions (CAPA)
The CAPA module is essential for addressing non-conformances and preventing their recurrence. It includes functionalities for:
- Identifying and documenting non-conformances
- Analyzing root causes
- Developing corrective and preventive action plans
- Implementing actions
- Verifying the effectiveness of actions
Change Control
This module manages changes to processes, equipment, documents, and other critical aspects of manufacturing. It includes:
- Submitting change requests
- Assessing the impact of proposed changes
- Approving or rejecting changes
- Implementing approved changes
- Tracking the implementation status
Market Complaints
The market complaint module handles customer complaints regarding the quality of products. It involves:
- Logging complaints
- Investigating complaints
- Taking corrective actions
- Communicating with customers
- Monitoring complaint resolution
Out of Specification (OOS) / Out of Trend (OOT) Management
This module deals with results that fall outside predefined specifications or show abnormal trends. It includes:
- Recording OOS/OOT results
- Investigating causes
- Implementing corrective actions
- Re-evaluating processes to prevent recurrence
Document Management
Document management is crucial for maintaining control over SOPs, batch records, and other critical documents. This module helps in:
- Creating and managing documents
- Version control
- Approval workflows
- Secure access and distribution
- Archiving and retrieval
Market Complaints
The market complaint module handles customer complaints regarding the quality of products. It involves:
- Logging complaints
- Investigating complaints
- Taking corrective actions
- Communicating with customers
- Monitoring complaint resolution

Benefits of QMS Software in Pharma Manufacturing
We all carry a lot of baggage, thanks to our upbringing. The majority of people carry with them, an entire series of self-limiting beliefs.
Get A QuoteTraceability
Provides complete traceability of actions and decisions, which is crucial during audits.
Vinfro's QMS Software
Vinfro's QMS software, launched in 2019, includes all these modules and is designed to address the critical data integrity issues in the pharma manufacturing industry. It integrates seamlessly with other systems, ensuring a cohesive approach to quality management.